From manufacturing and retail to healthcare and finance, more and more businesses are now recognizing the importance of continuous process improvement.
That’s because continuously improving your business’s processes, products, and revenue stream allows you to make the most of your company. This is also indicative of growth, which means that you are able to contribute more to the local economy.
Luckily, there are well-known frameworks that enable you and everyone in your business to implement business process improvement. These frameworks can also come in handy when building a continuous improvement plan for your company.
The Shewhart Cycle
Developed by 20th-century physicist, Walter A. Shewhart, the Shewhart Cycle follows an unending cycle of Plan – Do – Check – Act:
- Plan: Refers to identifying opportunities for improvement, as well as coming up with a continuous improvement plan for businesses.
- Do: This is where you test one of your tactics on a smaller scale. The key here is to test it on something where the results can be easily seen and measured.
- Check: Once you are done testing on a small scale, the next step is to evaluate and measure it. That way, you will know which part of the improvement plan sticks and which part needs some tweaking.
- Act: Depending on the outcome, this is the part of the Shewhart Cycle wherein you test your plan on a larger scale.
It may look easy, but since this is a cycle, it means that you will have to repeat the process if your plan fails. And once it succeeds, it is important that you measure and evaluate your plan and see how you can expand it and make it better.
Kaizen
Kaizen is a Japanese word that means “change for the better.”
This philosophy posits that everything can be improved, even if it is incremental. That’s because small, daily improvements are deemed desirable. Not to mention that it can eventually lead to bigger improvements in the long run.
When used in business process management, Kaizen is believed to improve the quality of work, streamline processes, reduce cost, and boost revenue. No wonder Toyota Production System uses it.
These two are just some of the popular improvement process methodologists. Now, it is time to know how you can build a continuous improvement plant or CIP for your own business.
Creating a CIP for Your Business
Since businesses are unique from one another, it can be challenging to emulate one company’s CIP. Fortunately, there are tips for a continuous improvement plan that are applicable across various industries.
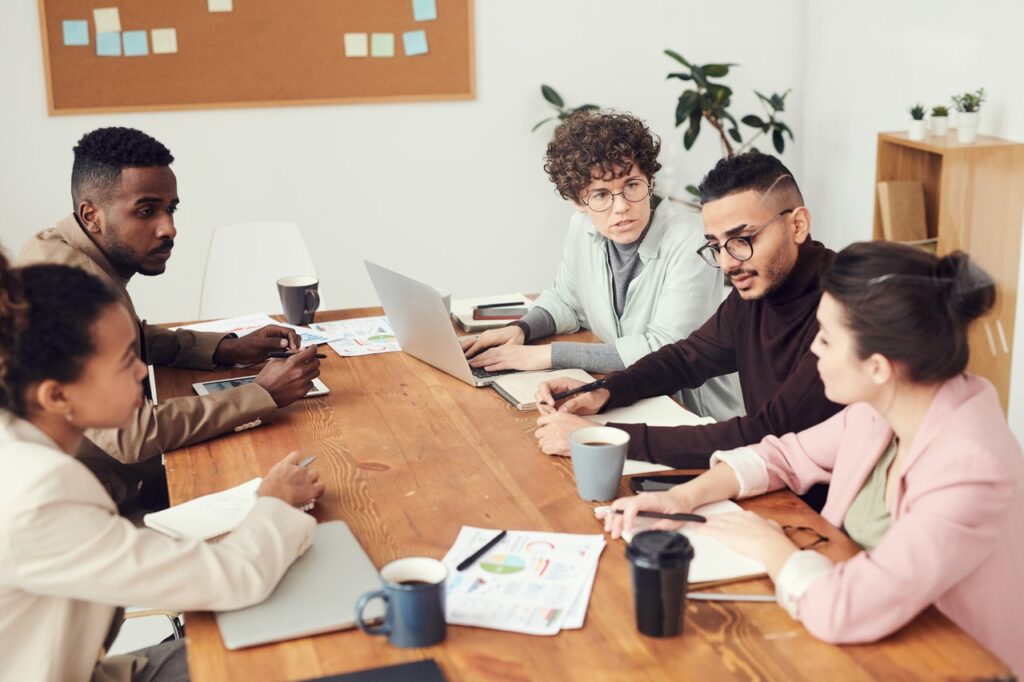
Photo courtesy of fauxels via Pexels. Creative Commons.
1. Start in the Leadership Team
In order for improvement to take place in your business, your entire leadership team should be on-board with it.
For one, they can help you identify opportunities for improvement. Second, it is important that they understand and support your intent to improve the business, as well as your plans on how to achieve it.
That’s because they have an overview of what is doing well and what is lacking in their department. It will also be easier to trickle down the information to everyone in your company with the help of your leadership team.
2. Run a Pilot Test
As mentioned in The Shewhart Cycle, you should test your plan on a small scale first.
Doing so allows you to monitor whether your plan will be effective or not. This also allows you to gather as much information as you can in order to properly address your employees’ concerns. Not to mention that middle managers can find it overwhelming to manage any drastic changes.
So, for instance, you want to streamline your human resources, you might want to test your plan within a small team of HRs first, such as those who are responsible for recruitment.
3. Get Your Employees on Board
Whether you are running a pilot test or implementing your new plan business-wide, it is important to keep your employees engaged.
You can do that by making sure that they understand the value of their participation. It can be as simple as telling them that you are testing a new improvement plan, and you will need their help to evaluate it.
4. Make Room for Mistakes
The beauty of creating your own CIP is that nothing is set to stone. Hence, it is important that you have room for mistakes when testing it.
After all, the key here is to perform trial and error in order to know how you can build a total quality management process. In case your plan fails, what’s important is that you identify the reason and then make a new plan.
As mentioned earlier, a CIP is an ongoing cycle. So when it fails, you will have to go back to square one. If it works, then you will have to measure and evaluate it, so you will know how you can implement the changes across your business.
5. Display Your Success
Sometimes, your CIP can bring subtle changes in your business that are small and hard to see. Hence, it is important that you review the improvements that you achieved because of your plan, and make sure that everyone in your company knows it.
In order to keep on satisfying your customers, it is important that you practice continuous improvement. And if building a CIP is something that you find challenging, ECCI is here to help you build an improvement process that is aligned with your company culture, attitude, and practices.